Delving into the World of Quality Control in Footwear: The Importance of QC for Shoes
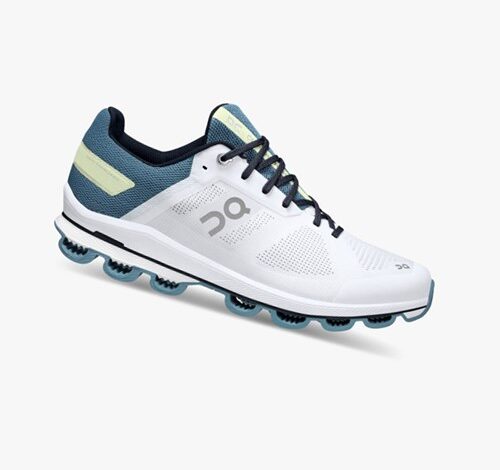
The Basics of Quality Control (QC) in Shoe Manufacturing Quality control (QC) in shoe manufacturing refers to the procedures that ensure shoes meet the desired quality standards. This process includes checking raw materials, monitoring production, and inspecting the final product. The QC process is critical in detecting faults early, preventing costly recalls, and ensuring customer satisfaction.
QC Tests: Ensuring the Durability and Comfort of Shoes QC tests vary from visual inspections to rigorous physical tests. Tests check various aspects of shoes, including stitching, bonding, color fastness, and abrasion resistance. Comfort factors, such as the shoe’s fit and material softness, are also evaluated. These tests ensure the shoes are aesthetically pleasing but also comfortable and durable.
Why QC Matters: The Impact of Quality Control on Shoe Brands Quality control directly affects a shoe brand’s reputation. Poor QC can lead to uncomfortable or poorly made shoes, resulting in dissatisfied customers and negative reviews. Conversely, good QC can boost a brand’s image, foster customer loyalty, and enhance overall market position.
Quality vs. Quantity: Balancing Mass Production and QC in the Shoe Industry In the face of mass production, maintaining high-quality standards can be challenging. Balancing quality with quantity is key for any shoe brand. Efficient QC processes ensure high production volumes don’t compromise the quality of the shoes. In a competitive market, a brand’s dedication to QC can make all the difference, showing commitment to quantity and, more importantly, quality.
The Basics of Quality Control (QC) in Shoe Manufacturing
Quality control (QC) is an essential element in shoe manufacturing, ensuring that the finished products meet set standards of quality, reliability, and performance. It’s a systematic process that involves various stages – from inspecting raw materials to examining the final product.
QC focuses on the raw materials used to create the shoes in the initial stages. Whether leather, fabric, or synthetic, materials are inspected for defects, color accuracy, and quality. Even minor imperfections at this stage can impact the final product, making this a critical step.
During manufacturing, QC measures include monitoring the craftsmanship, ensuring accurate sizing, and confirming that all components are assembled correctly. This stage often involves both automated checks and human inspections.
Once the shoes are assembled, final QC checks are conducted. These may include visual inspection, wear testing, and physical tests for bonding strength and material durability. This final stage ensures that the shoes look good, meet performance standards, and qc shoes are free from defects.
QC in shoe manufacturing is not a one-off process but a continuous one. It’s an essential part of manufacturing that helps ensure consistent quality, promotes customer satisfaction, and protects the brand’s reputation. Without rigorous QC measures, a shoe brand risks producing subpar products, leading to customer dissatisfaction, product returns, and, ultimately, brand image damage.
QC Tests: Ensuring the Durability and Comfort of Shoes
Quality Control (QC) testing plays a pivotal role in shoe manufacturing. It helps maintain high-quality standards and ensure the final products meet durability and comfort criteria.
One of the primary tests for durability is abrasion resistance. Shoes undergo tests using specialized machines that simulate the effect of prolonged usage on the shoe’s material. This test determines whether the shoes can withstand wear and tear over time.
The bonding strength is another crucial durability test. It checks the adhesion strength between shoe parts, like the sole and the upper. This ensures that the parts do not separate under stress, providing a durable, long-lasting product.
On the other hand, comfort tests focus on the shoe’s fit and flexibility. Fit testing involves trying the shoes on different foot shapes and sizes to ensure a comfortable fit for many consumers. Flexibility tests, meanwhile, check the shoe’s ease of movement. Shoes should bend and flex in certain areas to accommodate the foot’s natural motion.
Other tests may include color fastness (to ensure the color doesn’t fade or bleed), heel impact, and slip resistance. Each test provides valuable information about the shoe’s quality and performance.
QC tests provide the basis for any modifications or improvements in the shoe design or manufacturing process. Thus, they are crucial in ensuring that the shoes are visually appealing, durable, comfortable, and safe to use.
Why QC Matters: The Impact of Quality Control on Shoe Brands
Quality control (QC) is an essential pillar for shoe brands. Its impact is far-reaching, affecting a brand’s reputation, customer satisfaction, and profitability.
One of the most significant impacts of QC is on a brand’s reputation. In a highly competitive market, the quality of a product can set a brand apart. When a brand consistently delivers high-quality shoes, it can build a reputation for reliability and excellence. This can enhance brand loyalty, attract new customers, and positively affect the brand’s overall market position.
On the contrary, poor QC can have severe consequences. Shoes that fail to meet customers’ expectations regarding comfort, durability, or design can lead to negative reviews and harm the brand’s reputation. This can result in a loss of customer trust and, ultimately, decreased sales.
Furthermore, effective QC can contribute to cost efficiency. By identifying defects or issues early in the production process, brands can avoid costly recalls or the need to dispose of substandard products. This not only saves money but also helps protect the brand’s image.
Moreover, QC plays a crucial role in customer satisfaction. High-quality shoes that meet or exceed customers’ expectations can result in repeat purchases and positive word-of-mouth advertising.
In summary, quality control is not just a part of the shoe production process; it’s a critical factor that directly influences a brand’s success and sustainability in the market. Therefore, investing in effective QC practices is essential for any shoe brand aiming for long-term success.
Quality vs. Quantity: Balancing Mass Production and QC in the Shoe Industry
Like many others, the shoe industry faces the ongoing challenge of balancing quality with quantity. With the rise of fast fashion and the demand for affordable footwear, manufacturers often face pressure to increase output. However, mass production shouldn’t mean compromising quality control (QC).
Efficient QC systems are crucial in managing this balance. A robust QC process can catch faults early in production, ensuring that shoes do not fall short of quality standards, even in large quantities. By integrating QC into every step of the manufacturing process, shoe brands can ensure consistent quality across all products, regardless of volume.
Automation also plays a role in managing this balance. Automated QC systems can inspect large volumes of shoes quickly and accurately, identifying flaws that the human eye might miss. This allows for high-speed production without neglecting quality.
However, the human element remains essential. Experienced inspectors provide a level of understanding and nuance that machines can’t replicate. They can consider aspects like comfort and aesthetics, contributing to the overall quality of the product.
Ultimately, the key to balancing mass production and QC in the shoe industry is a combination of efficient processes, advanced technology, and skilled personnel. This balance allows brands to produce large volumes of shoes while maintaining customers’ expected quality. In a competitive market, a brand’s commitment to quality can be a significant differentiator, proving that quantity doesn’t have to come at the expense of quality.
Also, Read The Following: Craigslist San Diego